Concrete Pavement Joints
- Purpose
- Background
- Transverse Contraction Joints
- Longitudinal Joints
- Construction Joints
- Expansion Joints
- Joint Construction
- PURPOSE. To provide guidance and recommendations relating to the design and construction of joints in jointed Portland cement concrete pavements.
- BACKGROUND
- The performance of concrete pavements depends to a large extent upon the satisfactory performance of the joints. Most jointed concrete pavement failures can be attributed to failures at the joint, as opposed to inadequate structural capacity. Distresses that may result from joint failure include faulting, pumping, spalling, corner breaks, blowups, and mid-panel cracking. Characteristics that contribute to satisfactory joint performance, such as adequate load transfer and proper concrete consolidation, have been identified through research and field experience. The incorporation of these characteristics into the design, construction, and maintenance of concrete pavements should result in joints capable of performing satisfactorily over the life of the pavement. Regardless of the joint sealant material used, periodic resealing will be required to ensure satisfactory joint performance throughout the life of the pavement. Satisfactory joint performance also depends on appropriate pavement design standards, quality construction materials, and good construction and maintenance procedures.
- The most common types of pavement joints, which are defined by their function, are as follows
(2) Longitudinal Joint - a joint between two slabs which allows slab warping without appreciable separation or cracking of the slabs.
(3) Construction Joint - a joint between slabs that results when concrete is placed at different times. This type of joint can be further broken down into transverse and longitudinal joints.
(4) Expansion Joint - a joint placed at a specific location to allow the pavement to expand without damaging adjacent structures or the pavement itself.
TRANSVERSE CONTRACTION JOINTS. The primary purpose of transverse contraction joints is to control the cracking that results from the tensile and bending stresses in concrete slabs caused by the cement hydration process, traffic loadings, and the environment. Because these joints are so numerous, their performance significantly impacts pavement performance. A distressed joint typically exhibits faulting and/or spalling. Poor joint performance frequently leads to further distresses such as corner breaks, blowups, and mid-panel cracks. Such cracks may themselves begin to function as joints and develop similar distresses. The performance of transverse contraction joints is related to three major factors:
Joint Spacing. Joint spacing varies throughout the country because of considerations of initial costs, type of slab (reinforced or plain), type of load transfer, and local conditions. Design considerations should include: the effect of longitudinal slab movement on sealant and load transfer performance; the maximum slab length which will not develop transverse cracks in a plain concrete pavement; the amount of cracking which can be tolerated in a jointed reinforced concrete pavement; and the use of random joint spacings.
(1) The amount of longitudinal slab movement that a joint experiences is primarily a function of joint spacing and temperature changes. Expansion characteristics of the aggregates used in the concrete and the friction between the bottom of the slab and the base also have an effect on slab movement.
- (a) Joint movement can be estimated by the following equation:where:
= the expected change in slab length, in inches.
C = the base/slab frictional restraint factor (0. 65 for stabilized bases, 0. 8 for granular bases).L = the slab length, in inches.= the PCC coefficient of thermal expansion (see Table 1 for typical values).
= the maximum temperature range (generally the temperature of the concrete at the time of placement minus the average daily minimum temperature in January, in °F) .
= the shrinkage coefficient of concrete (see Table 2 for typical values). This factor should be omitted on rehabilitation projects, as shrinkage is no longer a factor.
Table 1Typical Values for PCC Coefficient of Thermal Expansion ( ) [1]
Type of Coarse Aggregate PCC Coeff. of Thermal Expansion (10-6/°F) Quartz 6.6 Sandstone 6.5 Gravel 6.0 Granite 5.3 Basalt 4.8 Limestone 3.8 - (b) While the above equation can be used to estimate anticipated joint movements, it may be worthwhile to physically measure joint movements in existing pavements. These measurements could provide the designer with more realistic design inputs.Table 2
Typical Values for PCC Coefficient of
Shrinkage () [1]
Indirect Tensile Strength (psi) PCC Coeff. of Shrinkage (in. /in. ) 300 (or less) 0.0008 400 0.0006 500 0.00045 600 0.0003 700 (or greater) 0.0002


(4) Random joint spacings have been successfully used in plain undoweled pavements to minimize resonant vehicle responses. When using random joint spacings, the longest slab should be no greater than 15 feet, to reduce the potential for transverse cracking. Some States are successfully using a spacing of 12'-15'-13'-14'. Large differences in slab lengths should be avoided.
(5) While they do not affect joint spacing, skewed joints have been used in plain pavements to provide a smoother ride. A skew of 2 feet in 12 feet is recommended, with the skew placed so that the inside wheel crosses the joint ahead of the outside wheel. Only one wheel crosses the joint at a time, which minimizes vehicle response and decreases stresses within the slab. Skewed joints are most commonly used when load transfer devices are not present. While skewed joints may be used in conjunction with load transfer devices, studies have not substantiated that skewing doweled joints improves pavement performance and are not recommended. Dowels in skewed joints must be placed parallel to the roadway and not perpendicular to the joints.
Load Transfer Across the Joint. Loads applied by traffic must be effectively transferred from one slab to the next in order to minimize vertical deflections at the joint. Reduced deflections decrease the potential for pumping of the base/subbase material and faulting. The two principal methods used to develop load transfer across a joint are: aggregate interlock; and load transfer devices, such as dowel bars. It is recommended that dowel bars be used.
(1) Aggregate Interlock. Aggregate interlock is achieved through shearing friction at the irregular faces of the crack that forms beneath the saw cut. Climate, and aggregate hardness have an impact on load transfer efficiency. It can be improved by using aggregate that is large, angular, and durable. Stabilized bases have also been shown to improve load transfer efficiency [14]. However, the efficiency of aggregate interlock decreases rapidly with increased crack width and the frequent application of heavy loads to the point that pavement performance may be affected. Therefore, it is recommended that aggregate interlock for load transfer be considered only on local roads and streets which carry a low volume of heavy trucks.
(2) Dowel Bars. Dowel bars should be used on all routes carrying more than a low volume of heavy trucks. The purpose of dowels is to transfer loads across a joint without restricting joint movement due to thermal contraction and expansion of the concrete. Studies have shown that larger dowels are more effective in transferring loads and in reducing faulting. It is recommended that the minimum dowel diameter be D/8, where D is the thickness of the pavement. However, the dowel diameter should not be less than 1 1/4 inches. It is also recommended that 18-inch long dowels be used at 12-inch spacings. Dowels should be placed mid-depth in the slab. Dowels should be corrosion-resistant to prevent dowel seizure, which causes the joint to lock up. Epoxy-coated and stainless steel dowels have been shown to adequately prevent corrosion.
Joint Shape and Sealant Properties
(1) The purpose of a joint sealant is to deter the entry of water and incompressible material into the joint and the pavement structure. It is recognized that it is not possible to construct and maintain a watertight joint. However, the sealant should be capable of minimizing the amount of water that enters the pavement structure, thus reducing moisture-related distresses such as pumping and faulting. Incompressibles should be kept out of the joint. These incompressibles prevent the joint from closing normally during slab expansion and lead to spalling and blowups.
(2) Sealant behavior has a significant influence on joint performance. High-type sealant materials, such as silicone and preformed compression seals, are recommended for sealing all contraction, longitudinal, and construction joints. While these materials are more expensive, they provide a better seal and a longer service life. Careful attention should be given to the manufacturer's recommended installation procedures. Joint preparation and sealant installation are very important to the successful performance of the joint. It is therefore strongly recommended that particular attention be given to both the construction of the joint and installation of the sealant material.
(3) When using silicone sealants, a minimum shape factor (ratio of sealant depth to width) of 1:2 is recommended. The maximum shape factor should not exceed 1:1. For best results, the minimum width of the sealant should be 3/8 inch. The surface of the sealant should be recessed 1/4 to 3/8 inch below the pavement surface to prevent abrasion caused by traffic. The use of a backer rod is necessary to provide the proper shape factor and to prevent the sealant from bonding to the bottom of the joint reservoir. This backer rod should be a closed-cell polyurethane foam rod having a diameter approximately 25 percent greater than the width of the joint to ensure a tight fit.
(4) When using preformed compression seals, the joint should be designed so that the seal will be in 20 to 50 percent compression at all times. The surface of the seal should be recessed 1/8 to 3/8 inch to protect it from traffic. Additional information can be obtained from FHWA Technical Paper 89-04, "Preformed Compression Seals" [5] for PCC pavement joints. "
LONGITUDINAL JOINTS
- Longitudinal joints are used to relieve warping stresses and are generally needed when slab widths exceed 15 feet. Widths up to and including 15 feet have performed satisfactorily without a longitudinal joint, although there is the possibility of some longitudinal cracking. Longitudinal joints should coincide with pavement lane lines whenever possible, to improve traffic operations. The paint stripe on widened lanes should be at 12 feet and the use of a rumble strip on the widened section is recommended.
- Load transfer at longitudinal joints is achieved through aggregate interlock. Longitudinal joints should be tied with tiebars to prevent lane separation and/or faulting. The tiebars should be mechanically inserted and placed at mid-depth. When using Grade 40 steel, 5/8-inch by 30-inch or 1/2-inch by 24-inch tiebars should be used. When using Grade 60 steel, 5/8-inch by 40-inch or 1/2-inch by 32-inch tiebars should be used. These lengths are necessary to develop the allowable working strength of the tiebar. Tiebar spacing will vary with the thickness of the pavement and the distance from the joint to the nearest free edge. Recommended tiebar spacings are provided in Table 3.
- Table 3 Maximum Recommended Tiebar Spacings
- Tiebars should not be placed within 15 inches of transverse joints. When using tiebars longer than 32 inches with skewed joints, tiebars should not be placed within 18 inches of the transverse joints.
- The use of corrosion-resistant tiebars is recommended, as corrosion can reduce the structural adequacy of tiebars.
- It is recommended that longitudinal joints be sawed and sealed to deter the infiltration of surface water into the pavement structure. A 3/8-inch wide by 1-inch deep sealant reservoir should be sufficient.
Transverse Construction Joints
(1) Transverse construction joints should normally replace a planned contraction joint. However, they should not be skewed, as satisfactory concrete placement and consolidation are difficult to obtain. Transverse construction joints should be doweled as described in paragraph 4b(2) and butted, as opposed to keyed. Keyed transverse joints tend to spall and are not recommended.
(2) It is recommended that transverse construction joints be sawed and sealed. The reservoir dimensions should be the same as those used for the transverse contraction joints.
Longitudinal Construction Joints
(1) The decision to use keyed longitudinal construction joints should be given careful consideration. The top of the slab above the keyway frequently fails in shear. For this reason, it is recommended that keyways not be used when the pavement thickness is less than 10 inches. In these cases, the tiebars should be designed to carry the load transfer.
2) When the pavement thickness is 10 inches or more, a keyway may be used to provide the necessary load transfer. If a keyway is to be used, the recommended dimensions are shown in Figure 1. Keyways larger than the one shown may reduce the concrete shear strength at the joint and result in joint failures. The keyway should be located at mid-depth of the slab to ensure maximum strength. Tiebars are necessary when using keyways. Consideration should be given to deleting the keyway and increasing the size and/or number of tiebars. The additional steel cost may be more than offset by the potential savings in initial labor and future maintenance costs.
EXPANSION JOINTS
- Figure 1 Recommended Keyway Dimensions
- (3) Tiebars should not be placed within 15 inches of transverse joints. When using tiebars longer than 32 inches with skewed joints, tiebars should not be placed within 18 inches of the transverse joints.
- (4) It is essential that the tiebars be firmly anchored in the concrete. Tiebars should be either mechanically inserted into the plastic concrete or installed as a two-part threaded tiebar and splice coupler system. It is recommended that periodic pullout tests be conducted to ensure the tiebars are securely anchored in the concrete. Attachment 2 describes a recommended testing procedure for tiebars.
- (5) Bending of tiebars is not encouraged. Where bending of the tiebars would be necessary, it is recommended that a two-part threaded tiebar and splice coupler system be used in lieu of tiebars. If tiebars must be bent and later straightened during construction, Grade 40 steel should be used, as it better tolerates the bending. It may be necessary to reapply a corrosion-resistant coating to the tiebars after they have been straightened. When pullout tests are performed, they should be conducted after the tiebars have been straightened.
- (6) It is recommended that longitudinal construction joints be sawed and sealed. The reservoir dimensions should be the same as those used for the longitudinal joints.
- Good design and maintenance of contraction joints have virtually eliminated the need for expansion joints, except at fixed objects such as structures. When expansion joints are used, the pavement moves to close the unrestrained expansion joint over a period of a few years. As this happens, several of the adjoining contraction joints may open, effectively destroying their seals and aggregate interlock.
- The width of an expansion joint is typically 3/4 inch or more. Filler material is commonly placed 3/4 to 1 inch below the slab surface to allow space for sealing material. Smooth dowels are the most widely used method of transferring load across expansion joints. Expansion joint dowels are specially fabricated with a cap on one end of each dowel that creates a void in the slab to accommodate the dowel as the adjacent slab closes the expansion joint, as shown in Figure 2.Figure 2 Expansion Joint Detail
- Pressure relief joints are intended to serve the same purpose as expansion joints, except that they are installed after initial construction to relieve pressure against structures and to alleviate potential pavement blowups. Pressure relief joints are not recommended for routine installations. However, they may be appropriate to relieve imminent structure damage or under conditions where excessive compressive stresses exist. Additional information can be obtained from the FHWA Pavement Rehabilitation Manual, Chapter 9.
7 . JOINT CONSTRUCTION
- Concrete Placement
(2) When using dowel baskets, the baskets should be checked prior to placing the concrete to ensure that the dowels are properly aligned and that the dowel basket is securely anchored in the base. It is recommended that dowel baskets be secured to the base with steel stakes having a minimum diameter of 0. 3 inch. These stakes should be embedded into the base a minimum depth of 4 inches for stabilized dense bases, 6 inches for treated permeable bases, and 10 inches for untreated permeable bases, aggregate bases, or natural subgrade. A minimum of 8 stakes per basket is recommended. All temporary spacer wires extending across the joint should be removed from the basket. Securing the steel stakes to the top of the dowel basket, as opposed to the bottom, should stabilize the dowel basket once these spacer wires are removed.
(3) Dowels should be lightly coated with grease or other substance over their entire length to prevent bonding of the dowel to the concrete. This coating may be eliminated in the vicinity of the welded end if the dowel is to be coated prior to being welded to the basket. The traditional practice of coating only one-half of the dowel has frequently resulted in problems, primarily caused by insufficient greasing and/or dowel misalignment. The dowel must be free to slide in the concrete so that the two pavement slabs move independently, thus preventing excessive pavement stresses. Only a thin coating should be used, as a thick coating may result in large voids in the concrete around the dowels.
(4) The placement of concrete at construction joints is particularly critical. Therefore, care must be taken to ensure that only quality concrete is used in their construction; i. e. , do not use the first concrete down the chute, nor the "roll" from the screed to construct this type of joint. The concrete used to construct these joints should be the same as for the remainder of the slab. The practice of modifying the mix at the joints is not recommended.
(5) Careful and sufficient consolidation of the concrete in the area of the joints is essential to good joint performance. Load transfer across a doweled joint is greatly affected by the quality of concrete consolidation around the dowels. Consolidation also has a direct relationship to concrete strength and durability. Concrete strength, in turn, has a significant effect on the amount of spalling that occurs at the joint.
(6) The placement of dowels should be carefully verified soon after paving begins. If specified tolerances are not being achieved, then an evaluation of the dowel installation, concrete mix design, and placement techniques must be made. Appropriate corrections should be made to the paving process to ensure proper alignment of the load transfer devices.
(7) When paving full-depth full-width, a mechanical prespreader and finishing machine in the paving train can be used to reduce drag and shear forces on the dowels.
(8) In cases where separate concrete placement is made adjacent to previously placed concrete, i. e. , truck climbing lanes or concrete shoulders being placed after mainline pavement, it is important that incompressibles do not enter the previously sawed transverse joint reservoir or crack that typically forms below the transverse joint reservoir. It is recommended that backer rod, tape, or other material be placed on the vertical face of the transverse joint at the edge of the pavement to prevent mortar from intruding into the existing joint. Failure to keep incompressibles out could prevent the joint from closing normally during slab expansion and may lead to delaminations near the edge of the previously placed concrete.
Sawing
(2) Time of initial sawing, both in the transverse and longitudinal directions, is critical in preventing uncontrolled shrinkage cracking. It is very important that sawing begin as soon as the concrete is strong enough to both support the sawing equipment and to prevent raveling during the sawing operation. All joints should be sawed within 12 hours of concrete placement. The sawing of concrete constructed on stabilized base must be sawed earlier. This is particularly critical during hot weather. Once sawing begins, it should be a continuous operation and should only be stopped if raveling begins to occur.
(4) For longitudinal joints, a minimum initial sawcut depth of D/3 is recommended to ensure cracking at the joint. The maximum sawcut depth should be such that the tiebars are not damaged. A final sawing that provides a 3/8-inch wide by 1-inch deep sealant reservoir should be sufficient.
(5) When a lengthy period is anticipated between the initial sawing of the joint and the final sawing and sealing, consideration should be given to filling the joint with a temporary filler. This filler material should keep incompressibles out of the joint and reduce the potential for spalling.
(6) The use of plastic inserts is not recommended. Although a few States have had success with these inserts, most States no longer allow their use. Improper placement of plastic inserts has been identified as a cause of random longitudinal cracking [2]. It is also very difficult to seal the joint formed by these inserts.
= [Eh3/12k(1-µ2) ]0. 25
DESIGN OF SLAB LENGTH
Studies have shown that pavement thickness, base stiffness, and climate affect the maximum anticipated joint spacing beyond which transverse cracking can be expected [2]. Research indicates that there is a general relationship between the ratio of slab length (L) to the radius of relative stiffness (_) and transverse cracking. The radius of relative stiffness is a term defined by Westergaard to quantify the relationship between the stiffness of the foundation and the flexural stiffness of the slab. The radius of relative stiffness has a lineal dimension and is determined by the following equation:

where
= radius of relative stiffness (in. )
- E = concrete modulus of elasticity (psi.)
- h = pavement thickness (in. )
- µ = Poisson's ratio of the pavement
- k = modulus of subgrade reaction (pci.)
Research data indicates that there is an increase in transverse cracking when the ratio L/
exceeds 5. 0. Using the criteria of a maximum L/
ratio of 5. 0, the allowable joint spacing would increase with increased slab thickness, but decrease with increased (stiffer) foundation support conditions. The relationship between slab length, slab thickness, and foundation support for a L/
ratio of 5. 0 is shown below.



Attachment 1: Design of Slab Length
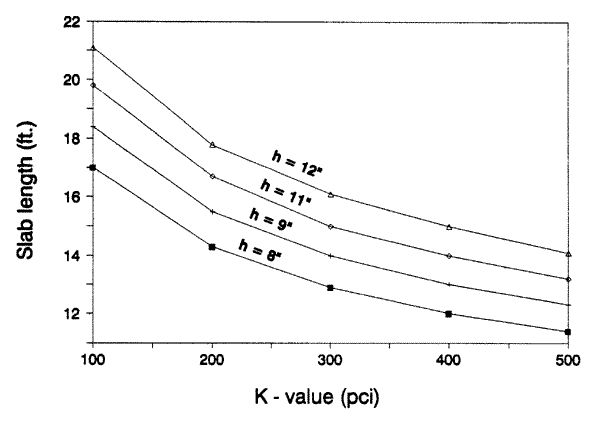
TIEBAR PULLOUT TESTS
Proper consolidation of the concrete around the tiebars is essential to the performance of longitudinal construction joints. Adjacent lanes should not be constructed until the project engineer has had opportunity to test the pullout resistance of the tiebars. Acceptance of the tiebars should be based on the results of the tests for resistance to pullout. The project engineer will select 15 tiebars from the first day's placement, after the concrete has attained a flexural strength of 550 psi. The tiebars will be tested to 12,000 lbs. or to a slippage of 1/32 inch, whichever occurs first. The average of the results of these pullout tests, divided by the spacing of the tiebars, will be used to determine the pullout resistance in lbs. per linear foot.
If the test results on the first day's placement are well within the test requirements shown below, additional testing will be at the discretion of the project engineer and will be based on comparison of the installation methods and spacings of the first day's placement with subsequent placements.
If the results of the pullout tests are less than the minimum requirements specified for the width of concrete being tied, the contractor shall install additional tiebars to provide the minimum average pullout resistance required, as directed by the project engineer. Testing of the supplemental tiebars will be at the discretion of the Engineer.
Tiebars shall be installed by methods and procedures such that the tiebars will develop the minimum average pullout resistance specified without any slippage exceeding 1/32 inch in accordance with the following table:
Tied Width of Pavement (Distance from Joint Being Constructed to Nearest Free Edge) | Average Pullout Resistance of Tiebars, lbs. /L. F. of joint, minimum. |
---|---|
12 feet or less | 2200 |
Over 12 feet to 17 feet | 3200 |
Over 17 feet to 24 feet | 4500 |
Over 24 feet to 28 feet | 5200 |
Over 28 feet to 36 feet | 6800 |
Over 36 feet | 9000 |
REFERENCES
1. "AASHTO Guide for Design of Pavement Structures 1986," American Association of State Highway and Transportation Officials, 1986.
2. "Performance of Jointed Concrete Pavements, Volume I, Evaluation of Concrete Pavement Performance and Design Features," Federal Highway Administration, FHWA-RD-89-136, K. D. Smith, D. G. Peshkin, M. I. Darter, A. L. Mueller, and S. H. Carpenter, March 1990.
3. Kelly, E. F. , "Application of the Results of Research to the Structural Design of Concrete Pavements," Public Roads, Volume 20, No. 6, August 1939.
4. "Portland Cement Concrete Pavement Evaluation System (COPES) ," M. I. Darter, J. M. Becker, M. B. Snyder, and
R. E. Smith, National Cooperative Highway Research Program Report 277, Transportation Research Board, 1985.
5. "Preformed Compression Seals," Federal Highway Administration, Pavement Division Technical Paper 89-04, 1989.
6. "Pavement Rehabilitation Manual," Chapter 9 - Pressure Relief in Concrete Pavement, Federal Highway Administration, FHWA-ED-88-025, 1988.
7. "1984 Standard Specifications for Construction," Michigan Department of Transportation, 1984.
8. "Design of Zero-Maintenance Plain Jointed Concrete Pavement," Federal Highway Administration, FHWA-RD-77-111, Vol. 1, M. I. Darter, 1977.
9. "Design, Construction, and Maintenance of PCC Pavement Joints," National Cooperative Highway Research Program, Synthesis of Highway Practice No. 19, Transportation Research Board, 1973.
10. "Concrete Pavement Construction - Inspection at the Paving Site, Portland Cement Association, EB085. 01P, 1980.
11. "Rigid Pavement Analysis and Design," Federal Highway Administration, FHWA-RD-88-068, K. W. Heinrichs, M. J. Liu, M. I. Darter, S. H. Carpenter, and A. M. Ioannides, 1989.
12. "Relationship of Consolidation to Performance of Concrete Pavements," FHWA-RD-87-095, D. A. Whiting and S. D. Tayabji, 1987.
13. "The Design of Plain Doweled Jointed Concrete Pavement,"
K. Kelleher and R. M. Larson, 4th International Conference on Concrete Pavement Design and Rehabilitation, 1989.
14. "Joint Design for Concrete Highway and Street Pavements," Portland Cement Association, IS059. 03P, 1980.
15. "The Benefits of Using Dowel Bars," Federal Highway Administration, Pavement Division Technical Paper 89-03, 1989.
16. "Performance of Jointed Concrete Pavements, Volume III, Summary of Findings," K. D. Smith, D. G. Peshkin, M. I. Darter, and A. L. Mueller, Federal Highway Administration, FHWA-RD-89-138, November 1990.
Updated: 04/07/2011
Post a Comment